Prof. Chris Damaren, Director, UTIAS, attributes the third year "Aerospace Control Systems" course he took with Peter Hughes as one of the reasons he does what he does. In describing Hughes as a teacher, Damaren states: “it is Peter's written exposition that sets him apart.”
As you will see in this remarkably interesting article, Hughes’s delightful way of communicating is evident. Plus, it didn’t hurt to have award-winning science writer Lydia Dotto at the typewriter.
Prof. Peter Hughes was the mastermind behind the successful design of Canadarm and Canadarm2 – he succeeded when US scientists told NASA it was not possible to succeed – and that story will be coming soon.
In the meantime, enjoy this fun, fascinating read!
Prof. Peter Hughes and Lydia Dotto died within months of each other, and both are worth reading about.
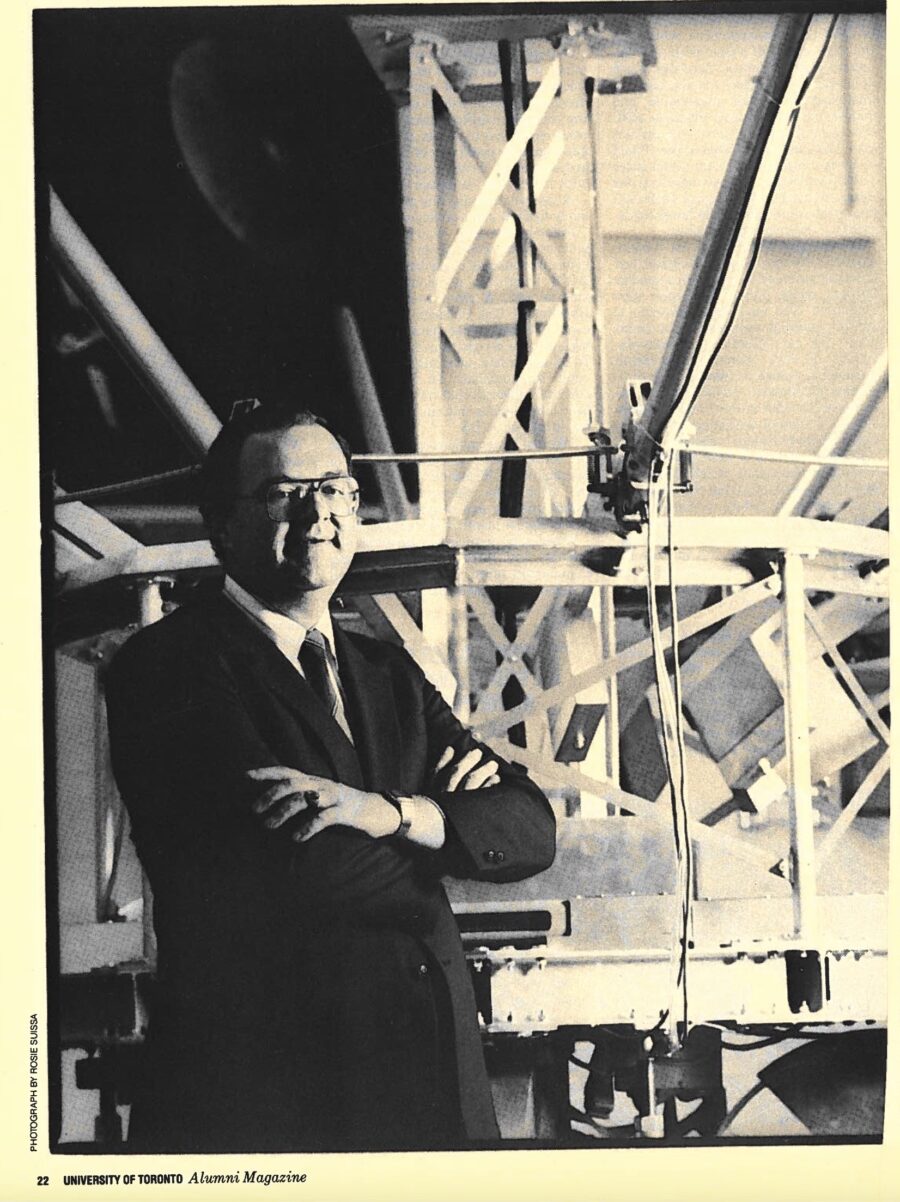
![Magazine clipping from University of Toronto Alumni Magazine, Autumn 1987
Headline: Kicking up Daisy: Peter Hughes’ contraption (which vaguely resembles the flower) mimics the vibrations and stresses that will be imposed on huge structures in space
Byline: Lydia Dotto
Photo: Professor Hughes, wearing a suit and tie, stands before the criss-crossing radial struts of Daisy.
Asking a group of scientists what space is like puts one in mind of the story about the blind men and the elephants. Everyone “sees” something different. A life support expert sees a harsh unforgiving environment that can kill a human being in minutes. A physiologist sees a more subtle but no less dangerous environment that can cause long-term health problems. A materials scientist sees an environment that can be exploited to make ultra-pure drugs, crystals and semiconductors.
One of the ways Peter Hughes sees space is as mathematical equations that define the position and motions of large structures in space. And he sees sleeping lions and restless tigers that need taming. Hughes, who is the University of Toronto’s Cockburn professor of engineering and a researcher at the Institute for Aerospace Studies, has built a device called Daisy that allows him to study in the laboratory the best methods for controlling and pointing large, flexible space structures such as antennae, sensors and solar panels. Examples of such structures include communications satellites and radar satellites used for remote sensing and surveillance. The research may also have some applications to the space station being built by the western world.
The need for this research has been prompted by the trend toward putting larger and larger structures in space – a trend that will be accelerated by the increasing use of shuttle-like vehicles and astronauts trained as “hard hats” to do assembly and construction work in space. Spacecraft of the future may be very large. Communications antennae may be as large as 150 to 200 metres in diameter, the size of a small city block. On earth, large usually equates with heavy, bulky and solid. Not so in space. In a zero-gravity environment, even very large structures are usually quite flimsy; many would collapse under their own weight on earth. Controlling such structures is no easy task, especially when pin-point accuracy is required, as in the case of a mobile communications satellite trying to beam signals to moving ships or aircraft. But flexible structures can be aggravatingly uncooperative. They bend, deform, vibrate, oscillate – and once they get going, they are hard to stop. Worse, if the control system is ineffective, these vibrations might escalate to the point of catastrophic instability resulting in serious damage to the structure.
This is where Daisy comes in. It’s not a wind tunnel. It does not physically resemble the space structures being studied. Instead, it consists of a circular array of metallic ribs radiating out from a base. (Its name is simply a whimsical reference to its vague high-tech resemblance to the petals of a flower.) What Daisy does do is emulate the behaviour of a space structure – the vibrations and motions that occur when the structure is subjected to forces by its control and pointing system. The same laws of motion apply on earth and in space, says Hughes. “We’re not pretending to test the ‘real’ structure, but we’re testing a structure that is behaving dynamically like the real structure.”
Each of Daisy’s two-metre aluminum ribs is attached to the circular base structure by a hinge that allows the rib to bob and weave freely in response to forces imposed on it. The ribs are connected to each other so the structure resembles the dish of an antenna. One of the ribs is equipped with a small thruster and a sensor to measure acceleration. Jogging the structure sets up slow, long-lasting vibrations that mimic behaviour of a much larger flexible space structure.
These studies provide a relatively inexpensive intermediate step between modelling a structure’s behaviour with computers and testing a prototype in space. Jumping straight from mathematical equations to hardware can result in “some rather expensive mistakes,” Hughes says.
The focus of the research is on the systems used to control space structures. While necessary – they point antennae and keep a satellite in proper orbit – they are also the major source of unwanted vibrations. Space is described as a harsh environment, but it is relatively benign in terms of the natural forces acting on structures. “The only thing bashing them around is the control system,” Hughes says.
There are three essential elements to the control system: the “eyes” or sensors that measure what the structure is doing; the “brain” or the computer that compares what the structure is doing and what it’s supposed to be doing, and issues commands to correct discrepancies; and the “muscle” or actuators such as motors, reaction wheels or thrusters, that respond to the computer’s commands. Control systems may over-correct. Flexible spacecraft vibrate in several different modes (directions) and correcting for one mode can start unwanted vibrations in others. And, due to light damping, over-correction can exacerbate the vibration problems. Control problems are getting worse because space structures are not only getting larger and flimsier, but the requirements for faster and finer control and pointing accuracy are becoming increasingly stringent.
Strategic Defense Initiative (SDI) technology is perhaps the ultimate case in point. Hughes says that while Daisy does not involve any work on SDI, the results will be available in the open literature and “could be” of some interest to SDI researchers. He adds that SDI represents an “extraordinarily difficult” control problem and “the whole thing only makes sense to [President Ronald] Reagan.”
Daisy is being used to study all three elements of the control system and Hughes hopes the research will lead to the development of new sensors and actuators for large space structures. The project has been funded by $600,000 in federal grants and contracts. The hardware was built by Dynacon Enterprises, a company founded by Hughes, under contract to the Department of Communications. The work of Hughes and his graduate students, and the cost of electronic equipment is being funded by a grant from the Natural Sciences and Engineering Research Council.
Through Dynacon, Hughes is also involved in two projects related to the international space station being built by the United States, Canada, Europe and Japan. The station, which will cost $20 billion US or more, is scheduled to go into operation in a 500-kilometre orbit n the mid-1990s. Canada’s contribution will be a Mobile Servicing System (MSS), an advanced computerized manipulator system that will help in the assembly and construction of the station structure and then be used for cargo-handling, servicing and refurbishment. Spar Aerospace is building the MSS. They’ve begun with building a sophisticated computer that will aid in the design and testing of the MSS. Dynacon has been sub-contracted to develop equations of motion on which the simulator’s computer programs will be based, including dynamic situations such as docking space shuttles to the station and using the manipulators to grapple cargo and to release satellites and other payloads into space.
Controlling the motion of manipulators is tricky. A manipulator must be capable of releasing a payload without imparting unwanted motions to it, and it must be able to grab large, multi-million dollar pieces of equipment without damaging them or itself. Dynacon is also doing another project for the National Research Council, involving studying an advanced manipulator that Hughes calls a “Trussarm.” This type of manipulator would have a lattice or truss structure not unlike those found on large construction cranes on earth. This is a very stable structure possessing great strength for its weight, so it’s expected to be very useful in space. Trussarm would be uniquely hinged in such a way that the arm could twist and turn and even curl around obstacles and into nooks and crannies, effective but posing many control problems. At present, there are no plans to build the device, but Hughes says “the Japanese are working on this like crazy.”](https://75.utias.utoronto.ca/images/_full/Image-2024-03-28-at-3.28-PM-1.jpeg)
![Magazine clipping from University of Toronto Alumni Magazine, Autumn 1987
Headline: Kicking up Daisy: Peter Hughes’ contraption (which vaguely resembles the flower) mimics the vibrations and stresses that will be imposed on huge structures in space
Byline: Lydia Dotto
Photo: Professor Hughes, wearing a suit and tie, stands before the criss-crossing radial struts of Daisy.
Asking a group of scientists what space is like puts one in mind of the story about the blind men and the elephants. Everyone “sees” something different. A life support expert sees a harsh unforgiving environment that can kill a human being in minutes. A physiologist sees a more subtle but no less dangerous environment that can cause long-term health problems. A materials scientist sees an environment that can be exploited to make ultra-pure drugs, crystals and semiconductors.
One of the ways Peter Hughes sees space is as mathematical equations that define the position and motions of large structures in space. And he sees sleeping lions and restless tigers that need taming. Hughes, who is the University of Toronto’s Cockburn professor of engineering and a researcher at the Institute for Aerospace Studies, has built a device called Daisy that allows him to study in the laboratory the best methods for controlling and pointing large, flexible space structures such as antennae, sensors and solar panels. Examples of such structures include communications satellites and radar satellites used for remote sensing and surveillance. The research may also have some applications to the space station being built by the western world.
The need for this research has been prompted by the trend toward putting larger and larger structures in space – a trend that will be accelerated by the increasing use of shuttle-like vehicles and astronauts trained as “hard hats” to do assembly and construction work in space. Spacecraft of the future may be very large. Communications antennae may be as large as 150 to 200 metres in diameter, the size of a small city block. On earth, large usually equates with heavy, bulky and solid. Not so in space. In a zero-gravity environment, even very large structures are usually quite flimsy; many would collapse under their own weight on earth. Controlling such structures is no easy task, especially when pin-point accuracy is required, as in the case of a mobile communications satellite trying to beam signals to moving ships or aircraft. But flexible structures can be aggravatingly uncooperative. They bend, deform, vibrate, oscillate – and once they get going, they are hard to stop. Worse, if the control system is ineffective, these vibrations might escalate to the point of catastrophic instability resulting in serious damage to the structure.
This is where Daisy comes in. It’s not a wind tunnel. It does not physically resemble the space structures being studied. Instead, it consists of a circular array of metallic ribs radiating out from a base. (Its name is simply a whimsical reference to its vague high-tech resemblance to the petals of a flower.) What Daisy does do is emulate the behaviour of a space structure – the vibrations and motions that occur when the structure is subjected to forces by its control and pointing system. The same laws of motion apply on earth and in space, says Hughes. “We’re not pretending to test the ‘real’ structure, but we’re testing a structure that is behaving dynamically like the real structure.”
Each of Daisy’s two-metre aluminum ribs is attached to the circular base structure by a hinge that allows the rib to bob and weave freely in response to forces imposed on it. The ribs are connected to each other so the structure resembles the dish of an antenna. One of the ribs is equipped with a small thruster and a sensor to measure acceleration. Jogging the structure sets up slow, long-lasting vibrations that mimic behaviour of a much larger flexible space structure.
These studies provide a relatively inexpensive intermediate step between modelling a structure’s behaviour with computers and testing a prototype in space. Jumping straight from mathematical equations to hardware can result in “some rather expensive mistakes,” Hughes says.
The focus of the research is on the systems used to control space structures. While necessary – they point antennae and keep a satellite in proper orbit – they are also the major source of unwanted vibrations. Space is described as a harsh environment, but it is relatively benign in terms of the natural forces acting on structures. “The only thing bashing them around is the control system,” Hughes says.
There are three essential elements to the control system: the “eyes” or sensors that measure what the structure is doing; the “brain” or the computer that compares what the structure is doing and what it’s supposed to be doing, and issues commands to correct discrepancies; and the “muscle” or actuators such as motors, reaction wheels or thrusters, that respond to the computer’s commands. Control systems may over-correct. Flexible spacecraft vibrate in several different modes (directions) and correcting for one mode can start unwanted vibrations in others. And, due to light damping, over-correction can exacerbate the vibration problems. Control problems are getting worse because space structures are not only getting larger and flimsier, but the requirements for faster and finer control and pointing accuracy are becoming increasingly stringent.
Strategic Defense Initiative (SDI) technology is perhaps the ultimate case in point. Hughes says that while Daisy does not involve any work on SDI, the results will be available in the open literature and “could be” of some interest to SDI researchers. He adds that SDI represents an “extraordinarily difficult” control problem and “the whole thing only makes sense to [President Ronald] Reagan.”
Daisy is being used to study all three elements of the control system and Hughes hopes the research will lead to the development of new sensors and actuators for large space structures. The project has been funded by $600,000 in federal grants and contracts. The hardware was built by Dynacon Enterprises, a company founded by Hughes, under contract to the Department of Communications. The work of Hughes and his graduate students, and the cost of electronic equipment is being funded by a grant from the Natural Sciences and Engineering Research Council.
Through Dynacon, Hughes is also involved in two projects related to the international space station being built by the United States, Canada, Europe and Japan. The station, which will cost $20 billion US or more, is scheduled to go into operation in a 500-kilometre orbit n the mid-1990s. Canada’s contribution will be a Mobile Servicing System (MSS), an advanced computerized manipulator system that will help in the assembly and construction of the station structure and then be used for cargo-handling, servicing and refurbishment. Spar Aerospace is building the MSS. They’ve begun with building a sophisticated computer that will aid in the design and testing of the MSS. Dynacon has been sub-contracted to develop equations of motion on which the simulator’s computer programs will be based, including dynamic situations such as docking space shuttles to the station and using the manipulators to grapple cargo and to release satellites and other payloads into space.
Controlling the motion of manipulators is tricky. A manipulator must be capable of releasing a payload without imparting unwanted motions to it, and it must be able to grab large, multi-million dollar pieces of equipment without damaging them or itself. Dynacon is also doing another project for the National Research Council, involving studying an advanced manipulator that Hughes calls a “Trussarm.” This type of manipulator would have a lattice or truss structure not unlike those found on large construction cranes on earth. This is a very stable structure possessing great strength for its weight, so it’s expected to be very useful in space. Trussarm would be uniquely hinged in such a way that the arm could twist and turn and even curl around obstacles and into nooks and crannies, effective but posing many control problems. At present, there are no plans to build the device, but Hughes says “the Japanese are working on this like crazy.”](https://75.utias.utoronto.ca/images/_full/Image-2024-03-28-at-3.29-PM.jpeg)
Pictured below is a photo of Daisy taken by Robert Lansdale.
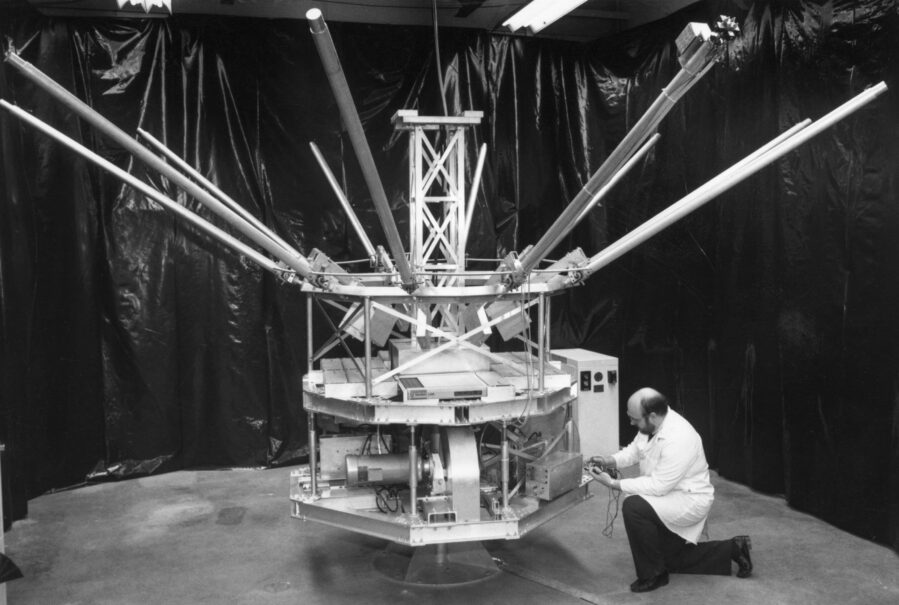